DEESING CATTLE HANDLING SYSTEMS
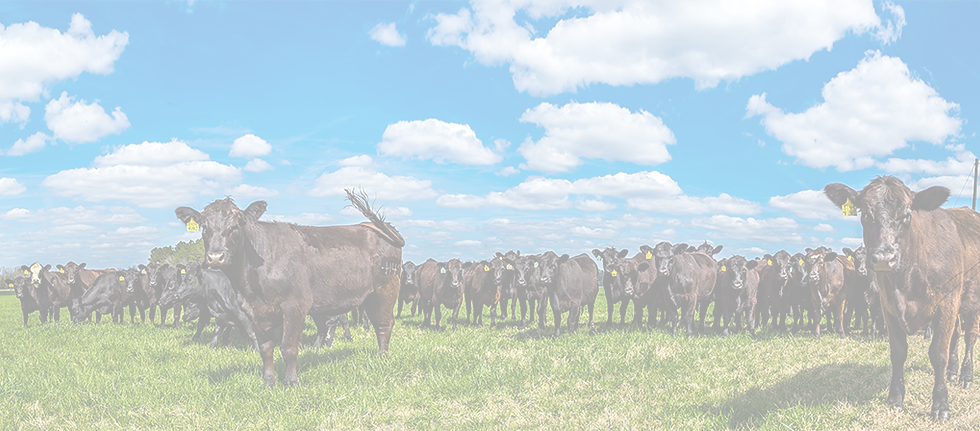
Over 20 years experience in research, design, and construction of cattle corral systems, custom cattle facilities, curved systems for happier, healthier animals.
Slaughter, Stockyard & Lairiage Systems for Beef Cattle
Click on the Photo To Enlarge and See Description

1. Large high speed Cattle slaughter plant serpentine. The facility is designed with a revolving double gate system in the crowd pen and two single file chutes (race). One chute is the primary; the second auxiliary chute is used in the case of an animal down in the primary chute. Each chute is 30-inches (76.20cm) wide, and 66-inches (167cm) high.
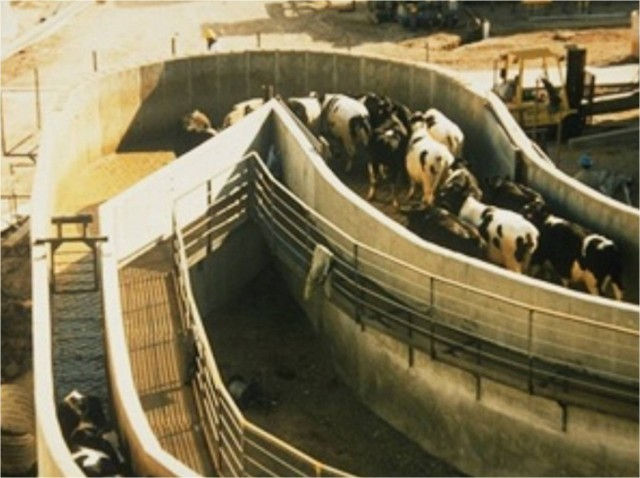
2. Half circle concrete crowd pen in large cattle slaughter plant. A single file chute 30-inch (76.20cm) wide and 66-inches high (167cm) is used. The round crowd pen is efficient because it takes advantage of the natural tendency of cattle to go back where they came from.

3. A 30 degree funnel into the single file chute does not look dead-ended to the cattle. The cattle enter the single file chute with a minimum of encouragement from the handler with the flag stick on the outside of the crowd pen. An auxiliary chute is used to prevent breaks in the line if an animal goes down in the primary chute. Handling in this facility is very efficient because skilled handlers are filling the crowd pen only half full.
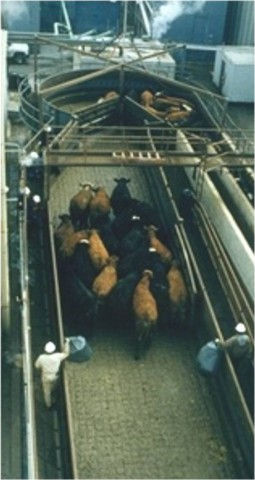
4. Small groups of cattle are moved from the stockyard (lairage) towards the crowding pen by handlers using plastic bags as a driving aid.
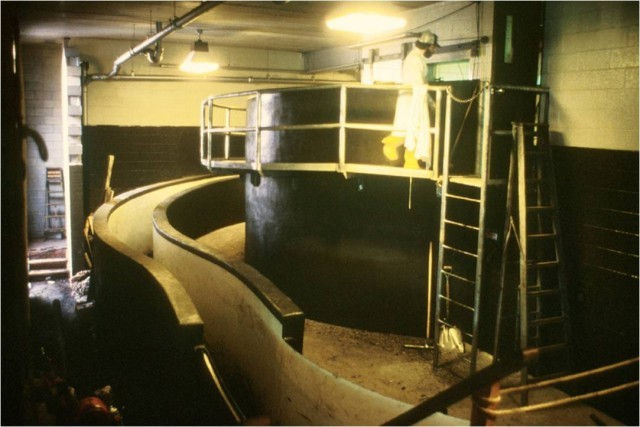
5. A restricted space cattle handling system in this medium sized slaughter plant with a concrete single file chute. This system works well because there is a 20-foot (6m) straight section of single file chute (race) before the first turn.
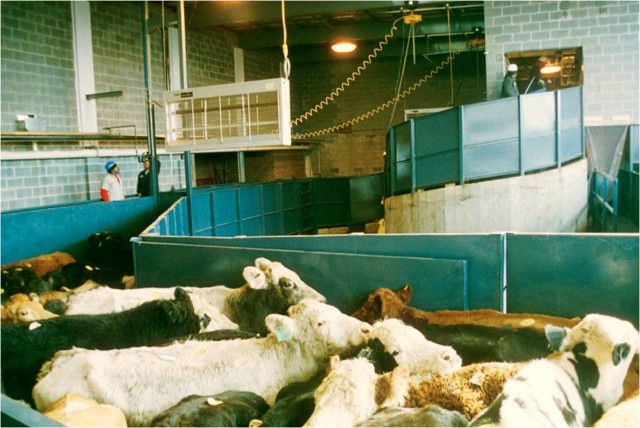
6. A medium sized slaughter plant handling system built with steel solid sided fences.
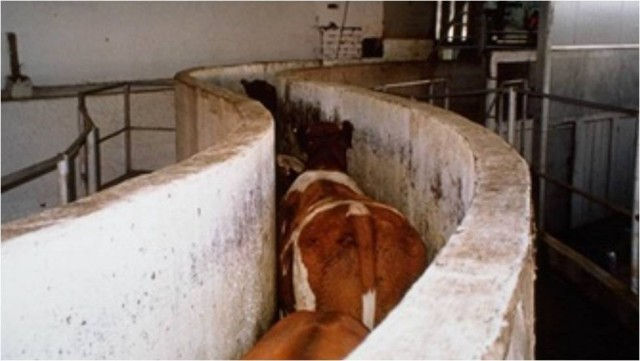
7. The 66-inch (167cm) high concrete walls in this single file chute prevent cattle from seeing people and other distractions ahead. Blocking vision keeps cattle calm in this beef slaughter plant.
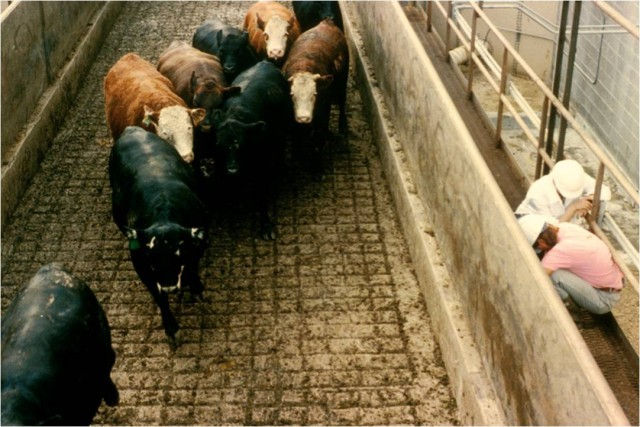
8. Deep grooved concrete floors prevent slipping and falling. Cattle get nervous on slippery floors. When cattle are being moved up this alley handlers are instructed to duck down below the height of the fence to keep cattle from balking.
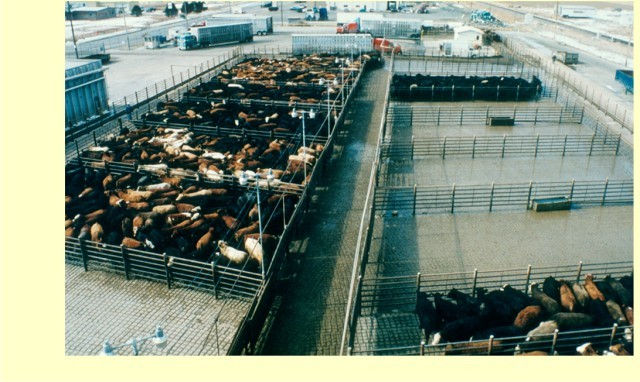
9. Herringbone pens in a large beef slaughter plant yard (lairage). Cattle enter the pens from the alleys on the outside, and exit towards the crowd pen through the center alley. All cattle movement is one-way. Cattle are held short term in the pens at a stocking density of 20 square feet per animal. A cattle water trough is placed between every other pen. The center alley is the high point. Pens are washed from the center alley towards a wash water drain on the outside of the entrance alleys.
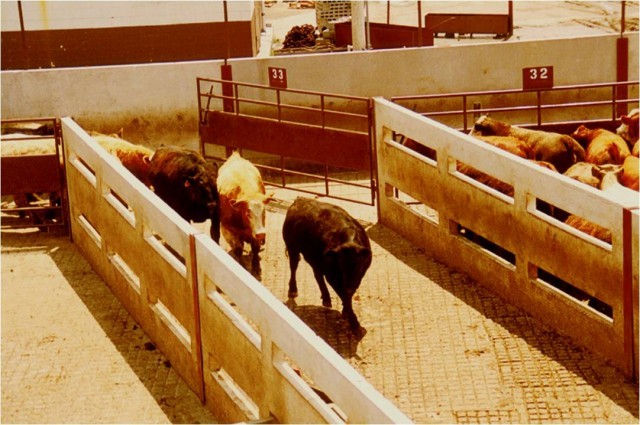
10. Pre-formed concrete walls are used in this large slaughter plant yard. Styrofoam blocks are placed in the concrete forms for the ventilation gaps.
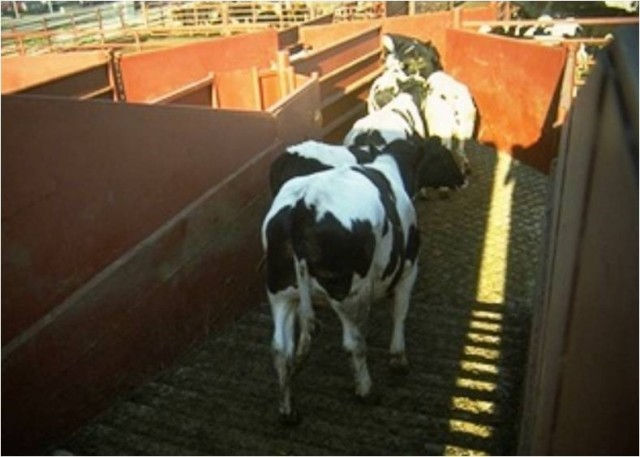
11. An 8-foot (2.4m) wide un-loading ramp. The ramp has 12-foot (30.48cm) wide steps 3-1/2-inch (89cm) high.

12. A center track restrainer in a large beef cattle slaughter plant. The cattle ride quietly because the curved shape of the conveyor is formed to fit their chest (brisket).

13. Light shining in cattle’s eyes causes balking. Pointing the light toward the door improved cattle movement.

14. Top rail was rolled at the machine shop on the radius of the crowd pen.
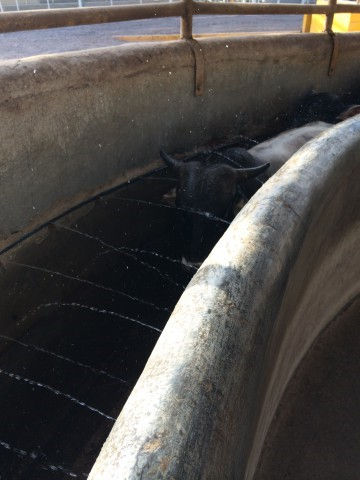
15. Side wash sprayers in single file chute.

16. Deep grooved concrete floors prevent slipping and falling. Shade cloth over pens keeps cattle cool, and a mist spray cleans cattle and prevents overheating.
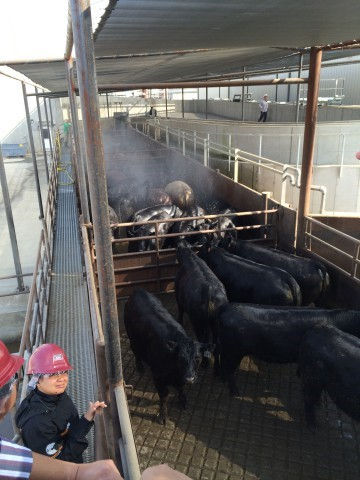
17. Over-head sprinklers wash cattle and cool them down on the way to the restrainer.

18. A Google Earth Image of a curved handling system at a high speed slaughter plant.

19. Hog slaughter plant. Solid fence is 42in. high and 10ga. Solid steel sheets are used for sides. Grooved concrete floors keep hogs from slipping and falling.

20. Overhead lighting prevents shadows that cause balking.

21. Concrete water tanks keep water cool in hot climates.
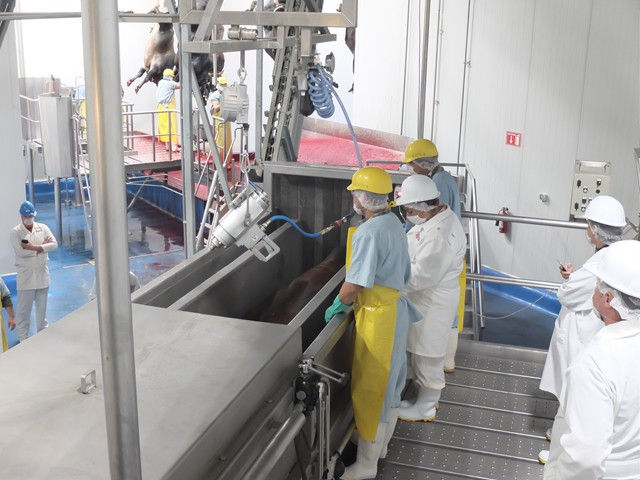
22. Center Track Restrainer in modern, high speed plant. The center track system provides the advantages of easier stunning and improved ergonomics because the stunner operator can stand closer to the animal. Either type of restrainer system is much safer for workers than a stunning box. Restrainer conveyors are recommended for all plants which slaughter over 100 head per hour.
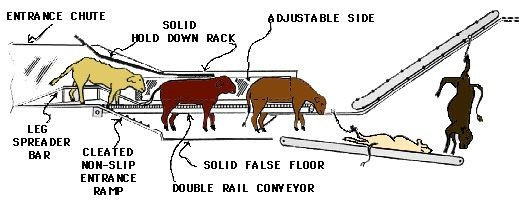
23. The center-track restrainer is a conveyor belt-like piece of machinery. Cattle straddle a track that lifts them up by the belly and propels them forward. It holds them steady during the final moment of slaughter, so that handlers can stun cattle with maximum effectiveness—a crucial moment of animal welfare.

24. First of its kind modern high speed slaughter plant in Mexico. The Grandin signature curved handling system can be seen in the bottom left.

25. Center Track Conveyor Entrance. The top of the conveyor is level with the floor of the entrance race. The animals walk down a cleated ramp which is on a 25 degree angle. The animal will walk in quietly if it does not slip. A common mistake many people make is to remove the cleats. Making an animal slide down the ramp is wrong. A ramp with a shallower angle, such as 15 to 20 degrees, can be used. An entrance ramp steeper than 25 degrees must never be used.

26. Stunning boxes should be narrow enough to prevent the animal from turning around. The floor should be non-slip so the animal can stand without losing its footing. It is much easier to stun an animal that is standing quietly. Only one animal should be placed in each stunning box compartment to prevent animals from trampling on each other. High solid sides at the entrance to the stunning box keep animals waiting in line calm.

27. Tall, concrete walls in slaughter plant are safe for cattle, block vision, and maintenance costs over steel construction are reduced. Grooved concrete floors provide a non-slip surface and prevent cattle from falling. Block gate in the alley is solid sided to prevent cattle from turning back towards other cattle moving up the alley. High speed slaughter plants require a steady un- interrupted flow of animals.
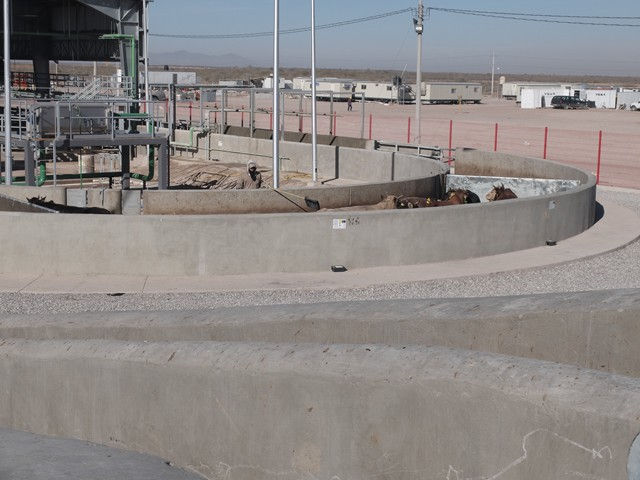
28. A raised concrete handler platform on both sides of the wide curved lane allow easy access to cattle by handlers working from either side.

29. Crowd Pen with dual revolving gates. The radius is 12 ft. (3.6m). Ratchet latches mounted on top of the wall spaced 2 ft. apart prevent the gate from being pushed back by cattle. The raised handler walkway is 42 in. (1066mm) down from top of 66 in. (1676) high solid concrete wall. Two man gates (457) allow easy access in or out of the crowd pen.

30. Back Stop gates in plant single file chutes (races). The chutes straight sided, 30 in. (762mm) wide, and 66 in. (1676) high. Steps in the chute provide the rise up to the plant. Standard steps in all ramps for cattle should be 12-18 in. (304-457mm) wide and 3-1/2 in. (89mm) high. A second single file chute is recommended in high speed plants to prevent delays if an accident occurs and an animal goes down in one chute. A selector gate at the entrance allows a handler to quickly switch sides.

31. As part of the USDA Humane Slaughter Act, “animals shall have access to clean water in all holding pens and, if held longer than 24 hours, access to feed.” Note the pipe rail on the cattle side to prevent cattle from defecating in tanks (this is a problem in parts of the world where bulls are raised.

32. Concrete walls make this double single file chute (race) system. The handler walkway is sloped making the repetitive climb easier, and more safe. The backstop gates are counter weighted and lift easily when cattle walk under.
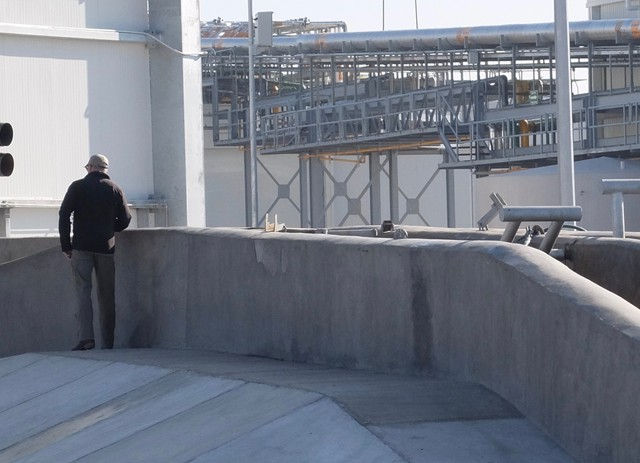
33. The handler walkway is 42 in. (1066mm) down from the top of the fence. This standard height is used in ranch facilities, feed yards, and slaughter plants, throughout the world. The person in this picture is 6 ft. (1828mm) tall. A 5 ft. 6 in. (1676mm) Mexican or Chinese is easily able to reach over the fence to touch cattle.
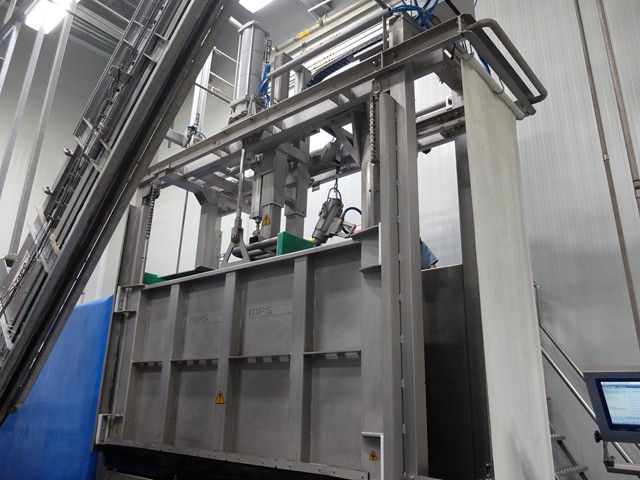
34. Modern stunning box with vertical drop out door. A hydraulic head holder inside the box hold the animal completely still for an accurate shot. Single shot kills are critical. World wide animal welfare organizations all have a zero tolerance policy for live cattle on the rail.

35. Before A dark entrance into slaughter plant stunning boxes is a common problem. When cattle move from outside to inside, the light-dark transition causes them to stop. Shadows in this transition must be avoided. Time of day effects occur in some facilities and shadows appear during certain times of day. Lighting can make a big difference.
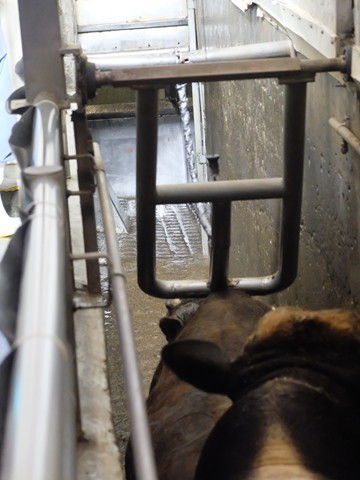
36. After Lighting the entrance to a knocking box can help cattle enter the box easier. In this picture, after installing the light one less person was required to move cattle from the race into the box. It is important that the light shine into the box and not into the cattle’s eyes.
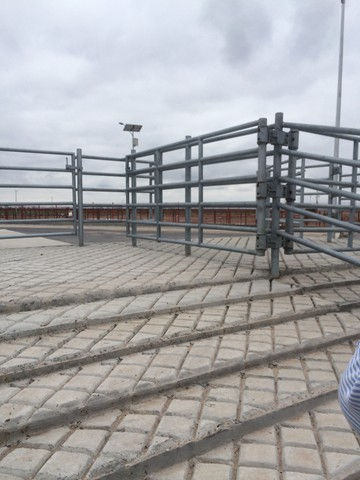
37. Slaughter plant receiving dock and ramp. Steps are 18 in. (457mm) wide by 3 ½ in. (89mm) high. Fourteen steps are required to reach ground level from the floor height of the truck. A 20 ft. (6 m) level area between the end of the truck and the steps is recommended to prevent cattle that run off a truck from falling down the steps.

38. A 12 ft. (3.6m) wide unloading area is recommended to provide cattle with an easy unobstructed exit off trucks, where accidents frequently occur. A single file is used for loading cattle, but cattle at slaughter plants off-load only.